PRODUZIONE DI ENERGIA ELETTRICA CON FORNO A SCARICA ELETTRICA DIRETTA.
ELECTRICITY PRODUCTION WITH DIRECT ELECTRIC DISCHARGE FURNACE.Con alcune prove fatte in laboratorio si è dimostrato che la scarica elettrica, la cui temperatura è di circa 10.000°K, riscalda il vapore d'acqua che si trova nelle sue vicinanze fino a 4.000°K e ne produce la scissione termica. Dopo la scissione, l'idrogeno e l'ossigeno prodotti si incendiano per l'alta temperatura dell'ambiente intorno alla scarica e producono calore. Detta combustione forma nuovamente vapore d'acqua che, per l'immediata vicinanza alla scarica elettrica, si scinde ancora in molecole di idrogeno / ossigeno provocando una nuova combustione. Ci si trova così con una continua scissione del vapore d'acqua in idrogeno e ossigeno che bruciando producono calore. La somma del calore prodotto dalla scarica elettrica e dalla combustione dell'idrogeno ottenuto con la scissione termica dell'acqua è superiore al calore richiesto per la produzione dell'energia elettrica necessaria per provocare la scarica elettrica.
With some tests made in the laboratory, it has been shown that the electric discharge, the temperature of which is about 10,000 °K, warms the water steam found in its vicinity up to 4,000 °K and produces its thermal splitting. After the thermal splitting, the hydrogen and oxygen produced by the electric discharge ignite due to the high temperature of the environment near the electric discharge and produce heat. After the said combustion it forms again steam of water which, for the immediate proximity to the electric discharge, a new thermal splitting is formed of the hydrogen/oxygen molecules, causing new combustion. This is a continuous thermal splitting of water steam in hydrogen and oxygen whose combustion produces heat. The sum of the heat produced by the electric discharge and by the combustion of hydrogen obtained with the thermal water splitting is higher than the heat required for the electricity production necessary to provoke the electric discharge.
Contacts: alzamarea@virgilio.it
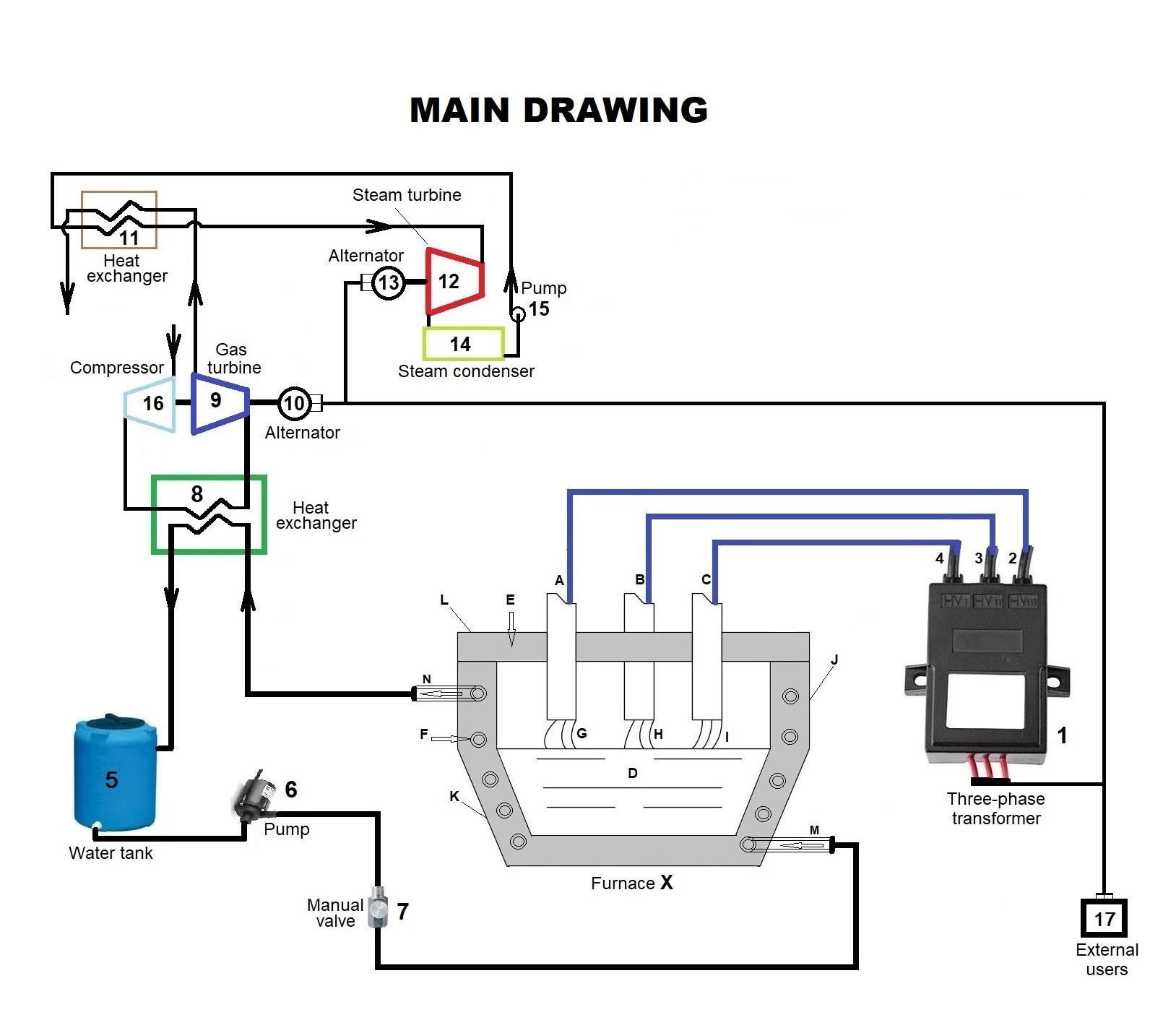
Contacts: alzamarea@virgilio.it
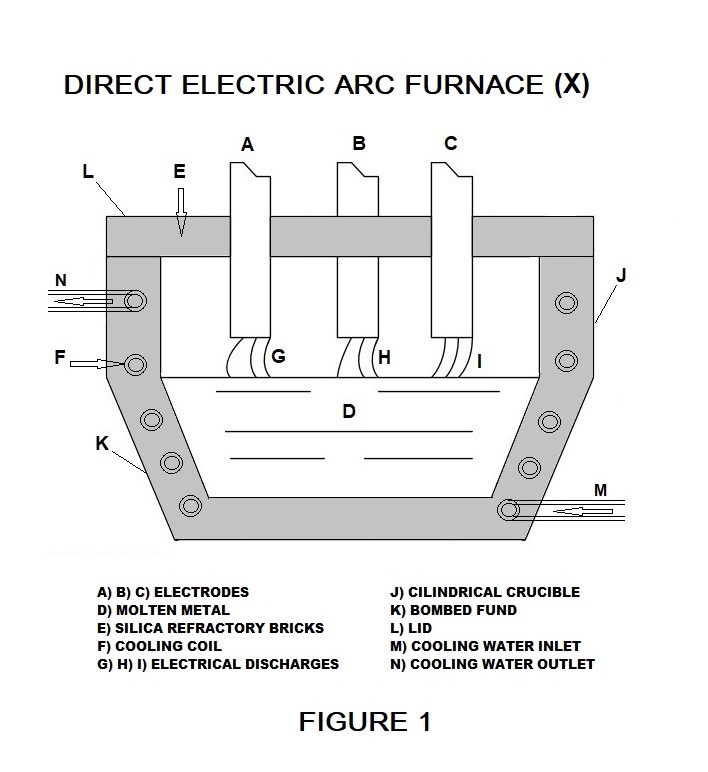
Contacts: alzamarea@virgilio.it
Le caratteristiche dell'acqua o del vapore d'acqua a pressione atmosferica sono:
Description
The characteristics of water or water vapor at atmospheric pressure are:
°K KJ / Kg physical state
- 293 84 water
- 373 420 water
- 373 2,676 steam
- 393 2,716 steam
- 1,273 4,642 steam
- 1,773 5,954 steam
- 2,273 7,377 steam
- 3,273 10,556 steam
- 4,000 13,146 steam
At a temperature of 2,273 °K, only three percent of all water is dissociated into hydrogen/oxygen atoms while at 3,273 °K more than half of the water molecules dissociate. To obtain the total thermal splitting of the water vapor, it must be heated to 4,000 °K. This temperature is impossible to reach as there are no materials that resist such temperature values. However, if the water vapor is conveyed towards an electric discharge, whose temperature is 10,000 °K, in the area of the molten metal close to the electric discharge the water vapor heats up to 4,000 °K and splits into distinct gases hydrogen-oxygen. The amount of water vapor with a temperature close to splitting that is found around the electric discharge is proportional to the intensity of the electric discharge itself.
In the furnaces for the production of steel, the direct electric discharge produces the heat necessary for the melting of the metal, attesting to the average internal temperature of around 3,000 °C. The proposed furnace (X) is represented graphically in figure 1 and is similar to the furnaces with direct electric discharge used in foundries to produce steel whose average internal temperature is about 3,000 °C. If during normal operation of the furnace (X), instead of adding steel, water is introduced, it is transformed into steam and reaches an average temperature of 3,000 °C absorbing heat by conduction as it is in direct contact with the molten metal (D ) and by radiation from electric discharges (G), (H), (I). Since the electric arcs (G), (H), and (I) reach a temperature of about 10,000 °C, the water vapor in their vicinity easily reaches 4,000 °K and dissociates into hydrogen and oxygen. The proximity of the electric discharges (G), (H), and (I) causes the immediate combustion of the two gases and their return to the state of water vapor at 3,000 °C.
The cooling coil (F) is made up of nickel-based steel and ceramic materials and can reach temperatures above 1,500 °C without losing its mechanical resistance characteristics. It is therefore possible to maintain the temperature inside the furnace (X) at 3,000 °C by adjusting the flow of cooling water with the valve (7) so that at the outlet of the furnace (N) there is water vapor at 1,500 °C. The availability of steam at this temperature allows it to be used to produce energy with a high ecological value such as electricity, hydrogen, etc., or used in large energy-consuming plants such as paper mills, foundries, glass industries, etc.
At first, to reach the thermal splitting conditions, it is necessary to heat the water from 293 °K (20 °C) to 4,000 °K and the electric discharge must provide 13,062 KJ / Kg of water (13,146 - 84). As we will see later, during the normal operation of the furnace (X) the heat of vaporization of the water must not be given as the steam never drops to the condensation temperature of the water but stops in the vapor state at the same predetermined average temperature. for the furnace (X).
The combustion of the gases produced by the thermal splitting of water produces heat defined by the higher calorific value of hydrogen which is 141,800 KJ / Kg. This value refers to the combustion products which do not undergo condensation and which are brought back to the initial temperature of the fuel and the combustive.
The splitting of water vapor into hydrogen-oxygen gas molecules occurs according to the reaction H2O → H2 + ½O2.
The calculation of the heat that can be produced with the combustion of hydrogen produced by the thermal splitting of a kilogram of water is defined as follows:
A mole of water weighs 18 and is composed of one mole of oxygen (molecular weight 16) and two moles of hydrogen (molecular weight 2); 1 kg of water is therefore composed of 0.89 kg of oxygen and 0.11 kg of hydrogen. The combustion of the hydrogen produced by the thermal dissociation of 1 kg of water is therefore theoretically capable of developing 141,800 * 0.11 = 15,598 KJ.
If in theory the internal temperature of the chamber where the phenomenon occurs at atmospheric pressure is fixed at 393 °K and theoretically it is supposed to bring all the water vapor produced by combustion to the predetermined temperature, in addition to 15,598 KJ / Kg, another 10,430 is obtained KJ / Kg (13.146-2.716) for cooling the water vapor. So in theory, with the combustion and cooling of gases up to 393 °K, 26.028 KJ / Kg (15.598 + 10.430) are obtained. To reach the thermal dissociation temperature again, however, the same quantity of heat obtained with the cooling of the gases must be returned with the electric discharge, i.e. 10,430 KJ / Kg.
If it is assumed to operate the plant at 1,273 °K, in addition to the heat of 15,598 KJ / Kg developed by combustion, it is necessary to add 8,504 KJ / Kg (13,146-4,642) available for cooling the water vapor to 1,273 °K. To bring it back to the temperature of thermal dissociation it is necessary to give the same energy quantity of 8,504 KJ / Kg with the electric discharge. It, therefore, appears that with the plant operated at 1.273 °K the energy to be supplied with the electric discharge is 8.504 KJ / Kg and the heat obtained from combustion and gas cooling is 24.192 KJ / Kg (15.598 + 8.504).
However, if a system similar to the direct arc furnace used in foundries for steel melting is used, it is possible to reach operating temperatures even higher than 3,273 °K (3,000 °C) and approach the thermal splitting temperature of the 'water. With it, in addition to the 15,598 KJ / Kg produced by the combustion of hydrogen and oxygen, 2,590 KJ / Kg (13,146-10,556) are also obtained for cooling to 3,273 °K. The theoretical total heat that can be taken from the furnace is therefore 18.188 KJ / Kg (15.598 + 2.590). It is then necessary to give the steam with the electric discharge of 2,590 KJ / Kg to obtain again the thermal splitting of the steam into hydrogen and oxygen.
temperatura calore speso calore ottenuto differenza rapporto
in cella °K con scarica KJ/Kg KJ/Kg KJ/Kg guadagno/spesa
1.273 8.504 24.192 15.598 2,84
3.273 2.590 18.188 15.598 7,00
In summary:
temperature heat thickness with heat obtained difference ratio
in cell °K electric arc KJ/Kg KJ / Kg KJ / Kg gain / expense
393 10.430 26.028 15.598 2,49
1.273 8.504 24.192 15.598 2,84
3.273 2.590 18.188 15.598 7,00
It is evident that the higher the operating temperature of the cell, the lower the heat to be supplied with the electric discharge to achieve the thermal dissociation of the water vapor. The ratio between heat obtained and electricity expenditure is also better. The problem, for an operation at high temperatures, lies in the ability of the materials to withstand them.
in cella °K per la scarica KJ/Kg dal sistema KJ/Kg KJ/Kg guadagno/spesa
1.273 25.770 24.192 -1.578 0,94
3.273 7.848 18.188 10.340 2,32
temperature heat thickness with heat obtained difference ratio
in cell °K electric arc KJ/Kg KJ / Kg KJ / Kg gain / expense
393 31.606 26.028 -5.578 0,82
1.273 25.770 24.192 -1.578 0,94
3.273 7.848 18.188 10.340 2,32
Nella figura 1 si rappresentano schematicamente i principali componenti del forno (X):L'alimentazione elettrica è del tipo trifase il cui centro stella è il fondo in acciaio (D) che durante il funzionamento diventa metallo fuso. Ciascuno dei tre archi (G), (H), (I) che si formano tra i rispettivi elettrodi di grafite (A), (B), (C) e il metallo fuso (D) rappresentano i carichi monofase del sistema. Il crogiolo cilindrico (J), il fondo bombato (K) e il coperchio (L) nella parte interna sono in carbonitruro d'afnio e la parte esterna in mattoni refrattari di silice. Il crogiolo (J) e il fondo (K) sono percorsi all'interno da una serpentina (F) in cui circola l'acqua di raffreddamento che entra nel forno (X) in (M) ed esce allo stato di vapore in (N). La serpentina (F) è a diretto contatto con la parete interna composta da carbonitruro d'afnio (HfCN) che possiede il punto di fusione a 4.200°C..
The use of a system referable to the first two examples that offer a system efficiency lower than 100% must be discarded, while it is important to highlight that with the use of a direct electric arc furnace operating at 3,000 °C, energy obtained is about double the energy spent for the production of the arc even though a very penalizing overall system efficiency of 33% has been set.
Figure 1 schematically shows the main components of the furnace (X):
The
power supply is of the three-phase type whose star center is the steel bottom
(D) which becomes molten metal during operation. Each of the three arcs (G),
(H), (I) that are formed between the respective graphite electrodes (A), (B),
(C), and the molten metal (D) represent the single-phase loads of the system.
The cylindrical crucible (J), the rounded bottom (K), and the lid (L) the internal part is made of hafnium carbonitride and the external part is made of silica refractory bricks. The crucible (J) and the bottom (K) are
crossed inside by a coil (F) in which the cooling water circulates which enters
the furnace (X) in (M) and exits in the vapor state in (N ). The serpentine (F) is in direct contact with the internal wall composed of Hafnium Carbonitride (HF CN) which has the highest melting point at 4,200 ° C.
- Per ottenere nel forno (X) gli archi elettrici (G), (H), (I) si utilizza un trasformatore trifase (1) che produce scariche elettriche in macro frequenza per evitare la corrosione degli elettrodi (A), (B), (C). I fili (2), (3), (4) del trasformatore (1) sono collegati rispettivamente agli elettrodi (A), (B), (C);
- Per assicurare la circolazione dell'acqua di raffreddamento nella serpentina (F) si dispone di una riserva d'acqua contenuta nel serbatoio (5). Da esso si aspira l'acqua con la pompa (6) e se ne regola il flusso con la valvola manuale (7). L'acqua che entra nel forno in (M), percorre tutta la serpentina (F) ed esce allo stato di vapore in (N). Dopo il raffreddamento prodotto dallo scambiatore (8), si rimette l'acqua nel serbatoio (5) alla stessa temperatura che aveva inizialmente ed è nuovamente disponibile per essere rimessa nel ciclo di raffreddamento del forno (X). Il calore assorbito dallo scambiatore di calore (8) viene utilizzato per produrre l'energia elettrica richiesta dal trasformatore (1) per produrre gli archi elettrici (G), (H), (I) nel forno (X). Siccome l'energia elettrica prodotta con il calore reso disponibile dallo scambiatore di calore (8) è superiore a quella richiesta dal trasformatore (1), si possono alimentare con l'energia residua utenze del tipo domestico o industriale (17);
- Per la produzione dell'energia elettrica si utilizza un sistema a ciclo combinato già presente sul mercato e composto da turbina a gas (9) e turbina a vapore (12). Per il ciclo della turbina a gas il compressore (16) aspira aria dall'ambiente e la comprime a circa 20 atmosfere. L'aria compressa viene riscaldata a 1.200°C con il calore assorbito al riscaldatore (8) e quindi mandata all'ingresso della turbina (9). Siccome l'aria in uscita dalla turbina (9) è ancora a temperatura elevata, prima di scaricarla nell'ambiente circostante viene raffreddata attraverso lo scambiatore di calore (11). Dallo stesso scambiatore (11) si trasmette il calore all'acqua proveniente dalla pompa (15) trasformandola in vapore d'acqua surriscaldato a 540°C e mandato alla turbina a vapore (12). Il vapore che esce dalla turbina (12) viene raffreddato con il condensatore (14) e torna in ciclo allo stato di liquido con la pompa (15). Sono collegati in modo assiale alla turbina ad aria (9) il compressore (16) e l'alternatore trifase (10). Ugualmente assiale alla turbina a vapore (12) è l'alternatore trifase (13) che insieme all'alternatore (10) consente di auto alimentare il forno ad arco (X) e fornire con l'energia elettrica in eccesso utenze esterne domestiche o industriali (17). Bisogna ricordare che i moderni turbogas funzionanti a ciclo combinato hanno un rendimento globale di circa il 50%.
The equipment shown graphically on the main drawing and described below is indispensable for the furnace (X) to work:
- To obtain electric arcs (G), (H), (I) in the furnace (X), a three-phase transformer (1) is used which produces electric discharges in macro frequency to avoid corrosion of the electrodes (A), (B), (C). The wires (2), (3), (4) of the transformer (1) are connected respectively to the electrodes (A), (B), (C);
- To ensure the circulation of the cooling water in the coil (F) there is a reserve of water contained in the tank (5). The water is sucked from it with the pump (6) and its flow is adjusted with the manual valve (7). The water that enters the furnace in (M), runs through the entire coil (F) and exits in the vapor state in (N). After the cooling produced by the exchanger (8), the water is returned to the tank (5) at the same temperature it had initially and is again available to be put back into the cooling cycle of the furnace (X). The heat absorbed by the heat exchanger (8) is used to produce the electrical energy required by the transformer (1) to produce the electric arcs (G), (H), (I) in the furnace (X). Since the electricity produced with the heat made available by the heat exchanger (8) is higher than that required by the transformer (1), domestic or industrial users (17) can be fed with the residual energy;
- A combined cycle system already present on the market is used for the production of electricity and consists of a gas turbine (9) and a steam turbine (12). For the gas turbine cycle, the compressor (16) sucks in air from the environment and compresses it to about 20 atmospheres. The compressed air is heated to 1,200 °C with the heat absorbed by the heater (8) and then sent to the turbine inlet (9). Since the air leaving the turbine (9) is still at a high temperature, before electric discharge it into the surrounding environment it is cooled through the heat exchanger (11). From the same exchanger (11) the heat is transmitted to the water coming from the pump (15) transforming it into water steam superheated at 540 °C and sent to the steam turbine (12). The steam that comes out of the turbine (12) is cooled with the condenser (14) and returns to the cycle in the liquid state with the pump (15). The compressor (16) and the three-phase alternator (10) are axially connected to the turbine (9). Equally axial to the steam turbine (12) is the three-phase alternator (13) which, together with the alternator (10), allows the arc furnace (X) to be self-powered and to supply domestic or industrial external users with excess electricity. (17). It must be remembered that modern combined cycle gas turbines have an overall efficiency of about 50%.
With the proposed plant, the fossil fuel used to feed the gas turbine is replaced with heat taken from the furnace (X) at 1,500 °C. Considering that the combined cycle plant efficiency is around 50%, 15,696 KJ are needed to produce 7,848 KJ of electricity for the dissociation of 1 Kg of water. From the furnace (X) 18,188 KJ are taken with the cooling coil (F) and 2,492 KJ of thermal energy are available for each Kg of dissociated water to produce electricity to be marketed for domestic or industrial uses (17).
It is important to point out that the furnace (X) with the equipment described above and represented in graphics by the main drawing is a completely closed system without by-products or effluents. The same argument is also valid for the combined cycle gas turbine which uses the heat subtracted from the furnace (X). The use of fossil fuels is thus avoided and the emission of gases harmful to the environment is eliminated. In this way, a zero-impact electricity production plant is obtained.
A further possibility of using the heat subtracted from the furnace (X) can be implemented for the production of hydrogen through the sulfur-iodine cycle. This system is environmentally friendly as it does not emit any product except hydrogen and oxygen. The system requires a minimum temperature of 850 °C and has an efficiency of about 50%. The detailed description of this use is referred to in another treaty.
The photographs below are extracted from the clips produced to document the experiment done in the laboratory with which the feasibility of the above is demonstrated. In them, it is noted that if the experiment is carried out in a free environment (figure 2), the water vapor and the dissociated gases are dispersed into the environment without triggering the combustion. If, on the other hand, the water vapor and the dissociated gases in the vicinity of the electric discharge are kept in a closed environment (figure 3), the combustion is triggered and repeats itself over and over. An electric discharge of a few watts was used for the experiment and there was considerable heating of the experimental cell and an important formation of condensation on the walls which prevented clear observation of the phenomenon. It is good to remember that a pure hydrogen flame in clean air does not appear bright because the radiations it emits are exclusively in the ultraviolet range.
Si cercano collaboratori. Per informazioni:
Contacts: alzamarea@virgilio.it
FIGURE 2
FIGURE 3